How to proceed kiosk project step by step
There are normally 5 steps to proceed kiosk project.
STEP 1 Evaluation and design
Each customer who approaches us has a project requirement or idea that they need to implement and deploy successfully. We evaluate the project requirements and uses our employees’ expertise to recommend certain components and/or different kiosk designs that will meet the functional and aesthetic needs of the customer. TopGood will create draft drawing to portray the finished product and the layout of proposed components. Additionally, the customer’s budget and time-line for project completion is in taken into consideration. Every detail is laid out on the table to make sure we have the best possible plan before entering the engineering stage of the project.
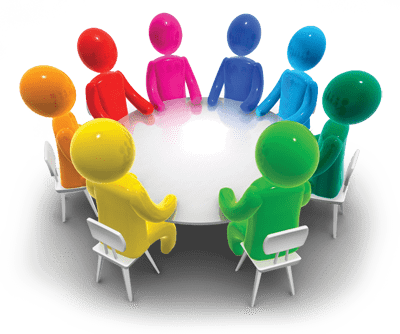
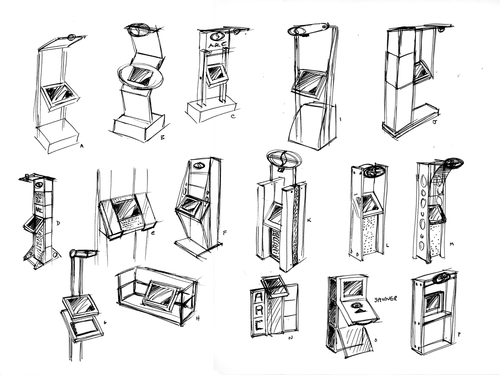
STEP 2 Engineering
This is to make the production drawing according to the 1st stage design, which will be done by our in-house engineering team. This results in finding ways to decrease cost, without taking away from the value of the finished kiosk product. Clear and open communication between TopGood and our client is paramount at this stage. All details are supplied in formal drawings showing exact layout of components, dimensions of every detail, how parts are accessible, etc. After the customer approved the drawing, we move forward to prototyping.
STEP 3 Prototype
Once the customer approved all the engineering details, we can move forward with in-house prototype fabrication. The importance of being able to carry out every process under one roof cannot be overstated, as it means we have complete control to keep a project within our clients’ budgets and time-lines. In fact, we even have customers come by and watch the metal being bent and welded together at times! The electronic components that were approved in the engineering phase are purchased and brought to our facilities and then assembled into the kiosk enclosure as they come off the production line. Since this is a first run at the kiosk solution, we sometimes have pieces that don’t fit perfectly, illustrating the TopGood advantage yet again. Because we fabricate in house, we are able to make most engineering “tweaks” immediately and re-fabricate parts quickly and easily, resulting in a prototype that meets the client’s requirements and expectations.
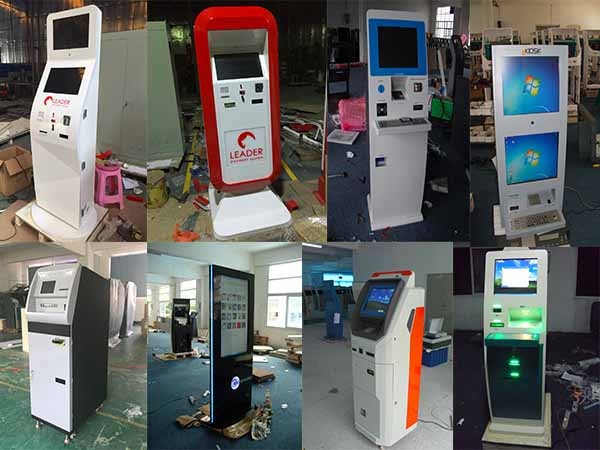
Metal enclosure production procedures
STEP 4 Production
Most customers take some time to test their prototype models and generally come back with other ideas and additions they want to implement. The majority of these are small changes and can be integrated into the production models instead of creating a brand new prototype. Production runs can be anywhere from 10 units to thousands. We work closely with our customers to ensure that we can meet their time-line requirements. At TopGood we understand the large number of working parts and complicated logistics that can come into play with sourcing all the materials necessary to complete a kiosk solution. We have dedicated project managers, purchasing managers and production managers all working together to manage this process successfully.
STEP 5 Shipment
Once products are coming off the production and assembly lines, we package them securely in our shipping department and schedule to ship cost effectively to customer locations. And we don’t stop there, we offer ongoing service and maintenance contracts to all of our clients.
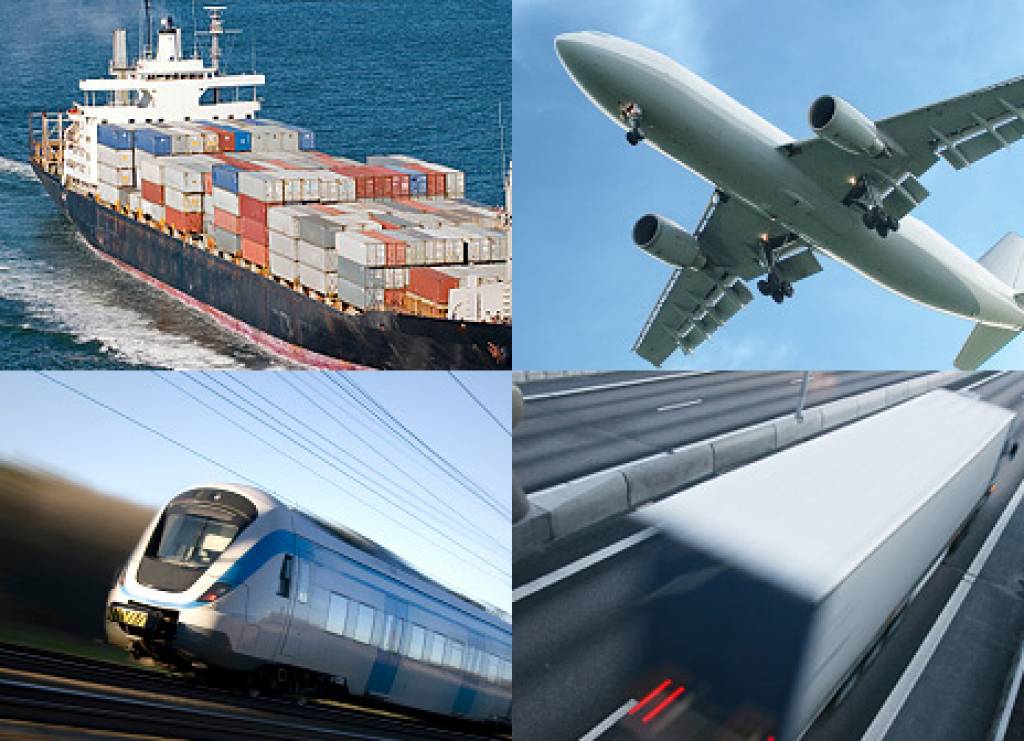